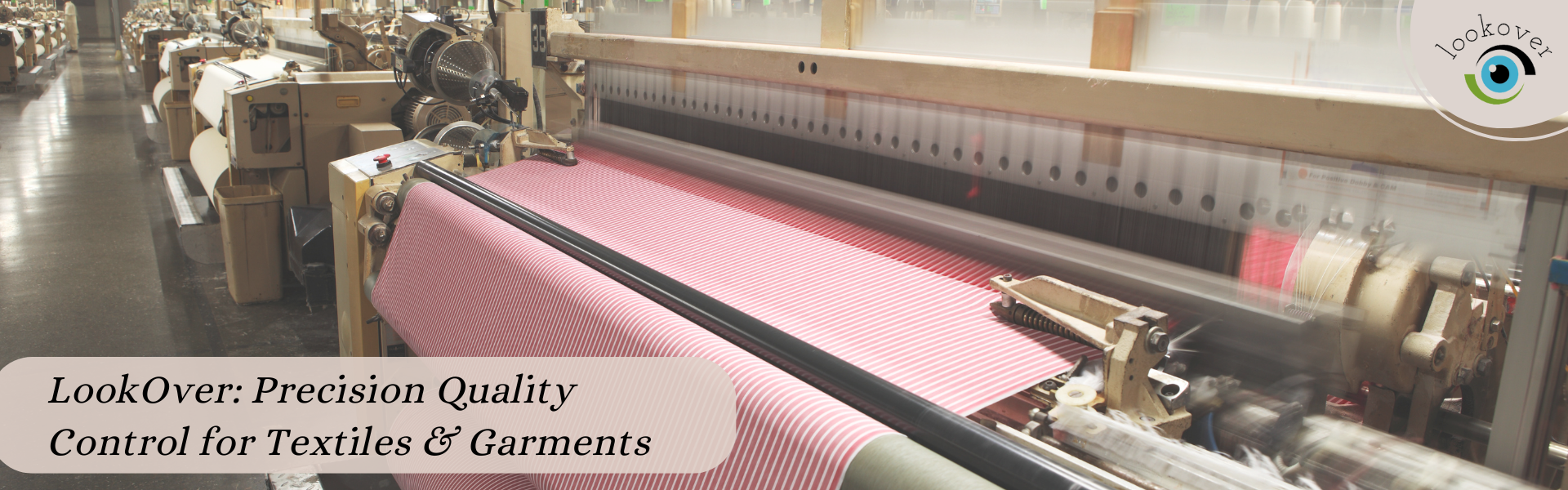
Quality Control in Textile Industry – A guide on how to upgrade
Key Issues in Textile Quality Control System
Quality control prevents faults in products and services while still being a work in progress. Quality control in the textile industry helps to catch defects before they make their way into the market.
In the textile industry, norms for quality control started during the craftsmanship era. Post industrialization and Taylorism, new quality control systems were used after World War 2, helping to streamline the process. However, these traditional quality control processes are fraught with inefficiencies. They lack accuracy as many due to over-dependency on human judgment and instinct.
Then was the arrival of quality control software where the majority of computations and documentation were given to a system. Now with AI, interactive UI, and the ability to scale fast, quality control software is changing the face of textile quality control.
1. Manually identifying defects
Manual inspection of defects like dyeing irregularity, holes, missing threads, etc., is a tedious task. They are hard to standardize due to their subjectivity. Only a trained pair of eyes can catch them effectively. The presence of such defects is non-negotiable for high-end brand selling in the EU, US, and the Middle East, leading to the rejection of entire lots.
2. Delays in data entry
Unlike quality management which is a system to infuse quality in the final product, quality control is an ongoing process during production. A defect caught at the beginning of the line is often not rectified till the end due to improper data entry. Manually entering data in checklists creates several human errors.
3. Tracking vendors
Tracking supplies from multiple vendors, and ensuring the same level of quality is a nightmare. When the same supply comes from multiple vendors, expecting a unified quality is a huge chore. Many buying houses lack a centralized system to track materials from multiple vendors. Using spreadsheets slows your system down when it is subjected to large amounts of data.
How does LookOver help – upgrade quality control to 2025
Create checklists and flow
Create checklists on all parameters and deploy them on mobile or desktop devices across the production line. This takes out human biases and keeps your quality control standardized. You can also save costs on training quality personnel, reducing dependency on trained quality controllers.
Centralized data
Quality control systems like Lookover help collect and store all product-related details in one place. Forget switching between a hundred spreadsheets and losing track of vital quality management information. Retrieve information easily with quick search options. Time to close the 100 tabs?
Communicate consistently
Talk to your vendor, to manage incoming and outgoing stocks. Reduce confusion of multiple conversation channels. If a defect is detected in quality control in line, instantly update your vendor regarding the same. This builds trust and long-term relationships with your vendors.
Plan your inspections
Inspections are a crucial part of quality control. Using quality control inspection software to create schedules and assign inspections is vital. Set reminders for assigned timelines so you do not miss out on any faults while still in production. Create a detailed protocol as per AQL levels regarding sampling size, defects type, inspection process, and how to document them.